Knowledge of Mechanical Engineering
facts, information, and skills acquired through experience or education; the theoretical or practical understanding of a subject about mechanical engineering.
Monday, 16 March 2020
Sunday, 9 June 2019
My First Journal Published
My first journal paper was published as a part of my Engineering project.
that is "DESIGN AND FABRICATION OF AUTOMATIC PAPER CUTTING MACHINE" in the Journal of Emerging Technologies and Innovative Research. I am happy and here is the information about that journal. It is the open access journal you can follow the link.
Cite This Article
"DESIGN AND FABRICATION OF AUTOMATIC PAPER CUTTING MACHINE", International Journal of Emerging Technologies and Innovative Research (www.jetir.org | UGC and issn Approved), ISSN:2349-5162, Vol.6, Issue 5, page no. pp269-274, May-2019, Available at : http://www.jetir.org/papers/JETIRBT06038.pdf
Wednesday, 30 August 2017
Auto Cad
Logo of Auto Cad
Ø Now days it is a most popular graphical
oriented designing product.
Ø Basically it was developed by sir auto desk
in 1972.
Ø The tool called r7.later Mr John from U.S.A. started a new organisation
called auto desk in 1980.hedevoleped a product called auto cad.
Ø The first famous product is auto cad 2000.it’s
the first graphical version. With the help of this version we can implement.
v Available versions
:-In auto cad we are having so many popular
versions they are :
I.
Auto cad 2000
II.
Auto cad 2003
III.
Auto cad 2005
IV.
Auto cad
2006&2007
V.
Auto cad
2010&2012
VI.
Auto cad 2014(windows
8 &above versions.)
v Hard
ware required:-To
install auto cad 2010&2012version we need the following hard ware
configuration.
I.
Windows
7 &above OS.
II.
Minimum
RAM capacity is 1GB.But recommended 2GB.
III.
We
need high resolution monitor.
IV.
Need
of a printer.(optional)
V.
Need
p4 or above C.P.U. But recommended dual core and above.
VI.
The
micro processor speed is not less than 1.2G.HZ.
v Available designing modes: - Basically we are having designing
methods like.
I.
Menu
bar.
II.
Command
bar.
Ø Menu
bar: - It is the
fully graphical oriented option .By using this option we can design type of
diagrams without knowing of any syntax .But it is not suitable for learners
.basically it is used by professional.
Ø Command
prompt: - This is
original concept of auto cad designing .it contains the following methods like:
I.
Standard
designing.
II.
Polar
method.
III.
Cortegen
method.
Ø Types of
commands: - In 2010&above versions the commands are mainly classified
into two major categories like:
I.
Administration
command.
II.
Designing
& modification command.
Ø Administration
commands: -
- Units : - With the help of this command we can display deferent designing measurements like:
1. Metric
conversion : -
1 centi meter = 10 milli meters
1
meter = 100 centimetres
1
kilo meter = 1000 meters
2.
Standard conversions : -
1 foot = 12 inches
1yard = 3 feat
1yard = 36 inches
1 mile = 1760 yards
3.
Metric conversions to standard conversions
: -
1 MM = 0.03937 INCHES.
1 CM = 0.39370 INCHES.
1 M = 39.37008 INCHES.
1 M = 3.028084 FEAT.
1 M = 1.09361 YARDS.
1 KM = 1093.6133 YARDS.
1 KM = 0.6213 M.
4.Standard
to metric : -
1 INCH = 2.54 CM
1 FOOT = 30.48 CM.
1YARD = 91.44 CM.
1YARD = 0.9144 M.
1MILE = 1609.344 M.
1 MILE = 1.609344 KM.



a)
Endpoint.
b)
Midpoint.
c) O Centre.
d)
Node.
e)
Quadrant.
f)
Intersection.
g)
Extant ion.
h)
Intersection.
i)
Perpendicular.
j)
Tangent
k)
Nearest.
l)
Apparent intersection.
m)
Parallel.

v Designing
commands : -
Ø Line
family : - in this
category we are having following commands like:
i.
Line.
ii.
M
line.
iii.
PL.
iv.
SPL.
v.
RAY.
vi.
X
Line.

a. Specify starting point.
b. Specify direction.
c. Specify length of the line.






Ø Text
operations: - To
implement all types of operations We are having the following commands like:
a. Text.
b. ED.
c. ST.
d. SC.
e. Mtext


ü BY double click also we can modify
text information.









Arc:
- We can design arc
related diagrams .We can design arc diagrams in two methods.
a) Manual.
b) Centre point specification.
Friday, 10 February 2017
Cams
Introduction:
A cam is a rotating machine element which gives
reciprocating or oscillating motion to another element known
as follower. The cam and the follower have a line contact
and constitute a higher pair. The cams are usually rotated at
uniform speed by a shaft, but the follower motion is predetermined
and will be according to the shape of the cam.
The cam and follower is one of the simplest as well as one
of the most important mechanisms found in modern
machinery today. The cams are widely used for operating
the inlet and exhaust valves of internal combustion engines,
automatic attachment of machineries, paper cutting machines,
spinning and weaving textile machineries, feed mechanism
of automatic lathes etc.
Classification of Followers:
The followers may be classified as discussed below :
1. According to the surface in contact. The followers,
according to the surface in contact, are as follows :
(a) Knife edge follower. When the contacting end of
the follower has a sharp knife edge, it is called a
knife edge follower, as shown in Fig. 20.1 (a). The
sliding motion takes place between the contacting
surfaces (i.e. the knife edge and the cam surface). It
is seldom used in practice because the small area of
contacting surface results in excessive wear. In knife
edge followers, a considerable side thrust exists
between the follower and the guide.
(b) Roller follower. When the contacting end of the follower is a roller, it is called a roller
follower, as shown in Fig. 20.1 (b). Since the rolling motion takes place between the
contacting surfaces (i.e. the roller and the cam), therefore the rate of wear is greatly reduced.
In roller followers also the side thrust exists between the follower and the guide. The
roller followers are extensively used where more space is available such as in stationary
gas and oil engines and aircraft engines.
(c) Flat faced or mushroom follower. When the contacting end of the follower is a perfectly
flat face, it is called a flat-faced follower, as shown in Fig. 20.1 (c). It may be noted that
the side thrust between the follower and the guide is much reduced in case of flat faced
followers. The only side thrust is due to friction between the contact surfaces of the follower
and the cam. The relative motion between these surfaces is largely of sliding nature but
wear may be reduced by off-setting the axis of the follower, as shown in Fig. 20.1 (f ) so
that when the cam rotates, the follower also rotates about its own axis. The flat faced
followers are generally used where space is limited such as in cams which operate the
valves of automobile engines.
Note : When the flat faced follower is circular, it is then called a mushroom follower.
(d) Spherical faced follower. When the contacting end of the follower is of spherical shape,
it is called a spherical faced follower, as shown in Fig. 20.1 (d). It may be noted that when
a flat-faced follower is used in automobile engines, high surface stresses are produced. In
order to minimise these stresses, the flat end of the follower is machined to a spherical
shape.
2. According to the motion of the follower. The followers, according to its motion, are of the
following two types:
(a) Reciprocating or translating follower. When the follower reciprocates in guides as the
cam rotates uniformly, it is known as reciprocating or translating follower. The followers
as shown in Fig. 20.1 (a) to (d) are all reciprocating or translating followers.
(b) Oscillating or rotating follower. When the uniform rotary motion of the cam is converted
into predetermined oscillatory motion of the follower, it is called oscillating or rotating
follower. The follower, as shown in Fig 20.1 (e), is an oscillating or rotating follower.
3. According to the path of motion of the follower. The followers, according to its path of
motion, are of the following two types:
(a) Radial follower. When the motion of the follower is along an axis passing through the
centre of the cam, it is known as radial follower. The followers, as shown in Fig. 20.1 (a)
to (e), are all radial followers.
(b) Off-set follower. When the motion of the follower is along an axis away from the axis of
the cam centre, it is called off-set follower. The follower, as shown in Fig. 20.1 ( f ), is an
off-set follower.
Note : In all cases, the follower must be constrained to follow the cam. This may be done by springs, gravity
or hydraulic means. In some types of cams, the follower may ride in a groove.
Classification of Cams:
Though the cams may be classified in many ways, yet the following two types are important
from the subject point of view :
A cam is a rotating machine element which gives
reciprocating or oscillating motion to another element known
as follower. The cam and the follower have a line contact
and constitute a higher pair. The cams are usually rotated at
uniform speed by a shaft, but the follower motion is predetermined
and will be according to the shape of the cam.
The cam and follower is one of the simplest as well as one
of the most important mechanisms found in modern
machinery today. The cams are widely used for operating
the inlet and exhaust valves of internal combustion engines,
automatic attachment of machineries, paper cutting machines,
spinning and weaving textile machineries, feed mechanism
of automatic lathes etc.
Classification of Followers:
The followers may be classified as discussed below :
1. According to the surface in contact. The followers,
according to the surface in contact, are as follows :
(a) Knife edge follower. When the contacting end of
the follower has a sharp knife edge, it is called a
knife edge follower, as shown in Fig. 20.1 (a). The
sliding motion takes place between the contacting
surfaces (i.e. the knife edge and the cam surface). It
is seldom used in practice because the small area of
contacting surface results in excessive wear. In knife
edge followers, a considerable side thrust exists
between the follower and the guide.
(b) Roller follower. When the contacting end of the follower is a roller, it is called a roller
follower, as shown in Fig. 20.1 (b). Since the rolling motion takes place between the
contacting surfaces (i.e. the roller and the cam), therefore the rate of wear is greatly reduced.
In roller followers also the side thrust exists between the follower and the guide. The
roller followers are extensively used where more space is available such as in stationary
gas and oil engines and aircraft engines.
(c) Flat faced or mushroom follower. When the contacting end of the follower is a perfectly
flat face, it is called a flat-faced follower, as shown in Fig. 20.1 (c). It may be noted that
the side thrust between the follower and the guide is much reduced in case of flat faced
followers. The only side thrust is due to friction between the contact surfaces of the follower
and the cam. The relative motion between these surfaces is largely of sliding nature but
wear may be reduced by off-setting the axis of the follower, as shown in Fig. 20.1 (f ) so
that when the cam rotates, the follower also rotates about its own axis. The flat faced
followers are generally used where space is limited such as in cams which operate the
valves of automobile engines.
Note : When the flat faced follower is circular, it is then called a mushroom follower.
(d) Spherical faced follower. When the contacting end of the follower is of spherical shape,
it is called a spherical faced follower, as shown in Fig. 20.1 (d). It may be noted that when
a flat-faced follower is used in automobile engines, high surface stresses are produced. In
order to minimise these stresses, the flat end of the follower is machined to a spherical
shape.
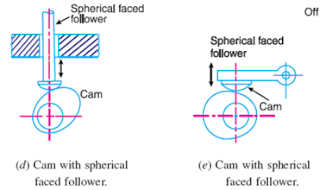
2. According to the motion of the follower. The followers, according to its motion, are of the
following two types:
(a) Reciprocating or translating follower. When the follower reciprocates in guides as the
cam rotates uniformly, it is known as reciprocating or translating follower. The followers
as shown in Fig. 20.1 (a) to (d) are all reciprocating or translating followers.
(b) Oscillating or rotating follower. When the uniform rotary motion of the cam is converted
into predetermined oscillatory motion of the follower, it is called oscillating or rotating
follower. The follower, as shown in Fig 20.1 (e), is an oscillating or rotating follower.
3. According to the path of motion of the follower. The followers, according to its path of
motion, are of the following two types:
(a) Radial follower. When the motion of the follower is along an axis passing through the
centre of the cam, it is known as radial follower. The followers, as shown in Fig. 20.1 (a)
to (e), are all radial followers.
(b) Off-set follower. When the motion of the follower is along an axis away from the axis of
the cam centre, it is called off-set follower. The follower, as shown in Fig. 20.1 ( f ), is an
off-set follower.
Note : In all cases, the follower must be constrained to follow the cam. This may be done by springs, gravity
or hydraulic means. In some types of cams, the follower may ride in a groove.
Classification of Cams:
Though the cams may be classified in many ways, yet the following two types are important
from the subject point of view :
1. Radial or disc cam. In radial cams, the follower reciprocates or oscillates in a direction perpendicular to the cam axis. The cams are all radial cams.
2. Cylindrical cam. In cylindrical cams, the follower reciprocates or oscillates in a direction parallel to the cam axis. The follower rides in a groove at its cylindrical surface. A cylindrical grooved cam with a reciprocating and an oscillating follower.
respectively.
Note : In actual practice, radial cams are widely used. Therefore our discussion will be only
confined to radial cams.
Terms Used in Radial Cams:
Fig. 20.3 shows a radial cam with reciprocating roller follower. The following terms are
important in order to draw the cam profile.
1. Base circle. It is the smallest circle that can be drawn to the cam profile.
2. Trace point. It is a reference point on the follower and is used to generate the pitch curve.
In case of knife edge follower, the knife edge represents the trace point and the pitch curve
corresponds to the cam profile. In a roller follower, the centre of the roller represents the trace point.
3. Pressure angle. It is the angle between the direction of the follower motion and a normal
to the pitch curve. This angle is very important in designing a cam profile. If the pressure angle is
too large, a reciprocating follower will jam in its bearings.
4. Pitch point. It is a point on the pitch curve having the maximum pressure angle.
5. Pitch circle. It is a circle drawn from the centre of the cam through the pitch points.
6. Pitch curve. It is the curve generated by the trace point as the follower moves relative to
the cam. For a knife edge follower, the pitch curve and the cam profile are same whereas for a
roller follower, they are separated by the radius of the roller.
7. Prime circle. It is the smallest circle that can be drawn from the centre of the cam and
tangent to the pitch curve. For a knife edge and a flat face follower, the prime circle and the base
circle are identical. For a roller follower, the prime circle is larger than the base circle by the radius
of the roller.
8. Lift or stroke. It is the maximum travel of the follower from its lowest position to the
topmost position.
Fig.
Subscribe to:
Posts (Atom)
About the author
Hi ! Everyone. This is Venkata Surya Mohan Krishna DME., B TECH., This blog consists of my th...
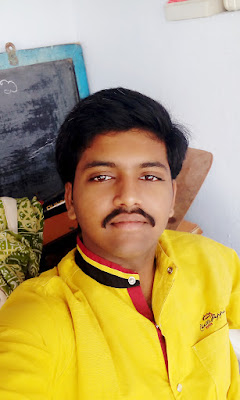
-
Introduction: A cam is a rotating machine element which gives reciprocating or oscillating motion to another element known as follower...
-
My first journal paper was published as a part of my Engineering project. that is "DESIGN AND FABRICATION OF AUTOMATIC PAPER CUTT...
-
Introduction: The Pelton wheel is an impulse type water turbine. It was invented by Lester Allan Pelton in the 1870s. The Pelton wheel ...